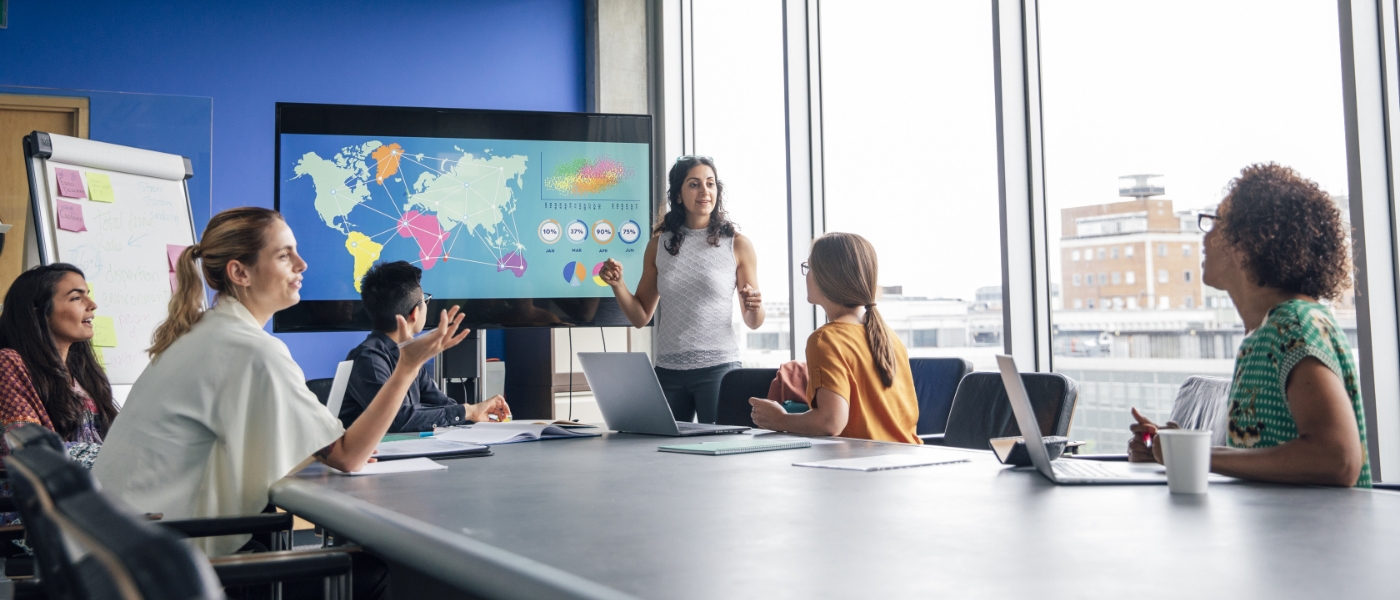
Employee Safety
Basic Approach to Employee Safety
We strive to create a safe and healthy work environment where all employees can be satisfied and engaged in their work. An important responsibility for any company should be to create an environment where employees with a diverse background can work in a healthy and rewarding way, maximize their individual abilities, and grow while working hard together with respect for all. This also is the starting point for growth.
Industrial Safety and Health Policy
Basic Philosophy
We are committed to maintaining a sound working environment that engages all employees to promote safety and health in the workplace, which we believe is an important principle of a successful business.
Action Plan Guidelines
- We observe all government regulations as well as company and specific work rules that pertain to industrial safety and health.
- We aim to achieve zero industrial accidents by accurately identifying hazardous and harmful factors through near-miss incidents and risk assessments, and by promoting activities to reduce the risks of such hazards.
- We are committed to continued learning to enhance knowledge, awareness and activities related to industrial safety and health.
- We maintain and promote mental health in all personnel by facilitating healthy and constructive communication in the workplace.
- We keep all personnel informed and actively engaged in maintaining the highest standards of industrial safety and health.
Occupational Health and Safety Promotion System
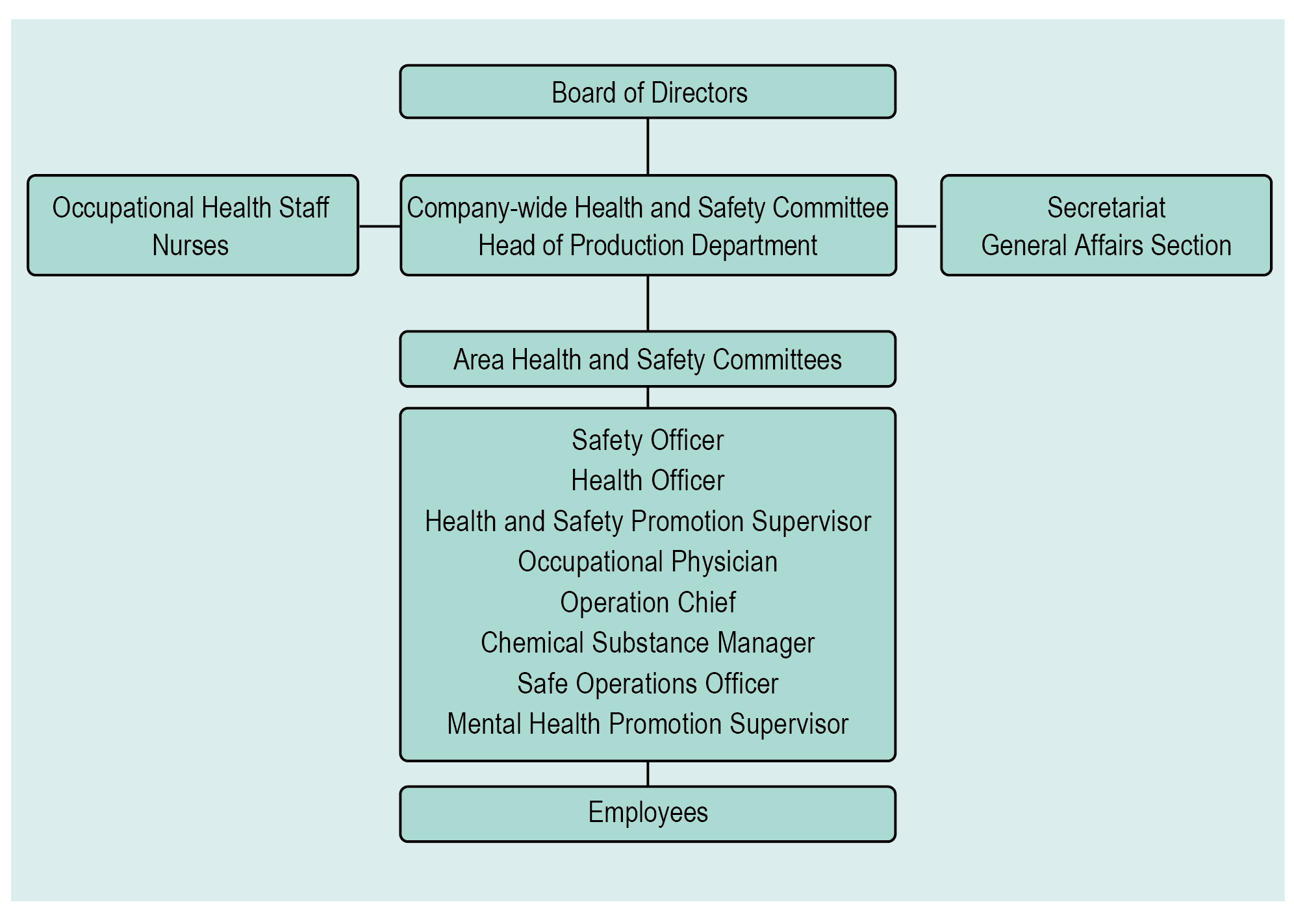
Initiatives to Ensure Safety in the Workplace
We regard accidents at any of our work locations as a crucial issue. Nagase Viita therefore conducts training based on the occupational safety plan we formulate each year with the aim of enabling our employees to acquire the knowledge and skills they require. Through these activities, we are working to foster a culture of safety throughout the whole Company to create an accident-free workplace.
Safety Training
◇ Training Topics
- Sharing of disaster case studies based on past cases throughout the whole Company
- Sharing of disaster information among the NAGASE Group manufacturing companies
- Workplace inspections and legal training by occupational health and safety consultants
- Workplace inspections and workplace improvements by industrial physicians
- Standardization and company-wide rollout of inspection record format
- Educational activities for disaster prevention at each district health and safety committee
- Talk given by local fire department
- Heat stroke prevention seminar
- Risk assessment case study training
- Verifying risk assessment activities and an exploration of good practices
- A look at near-miss incidents, past accidents, and risk prediction
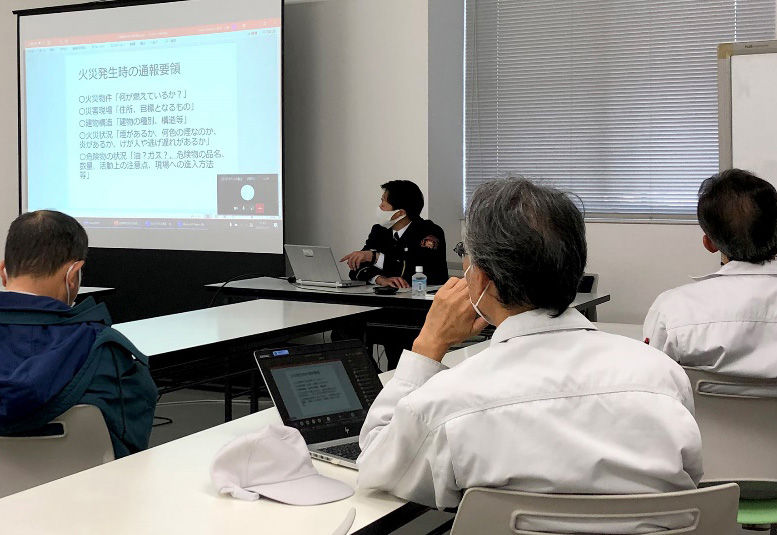
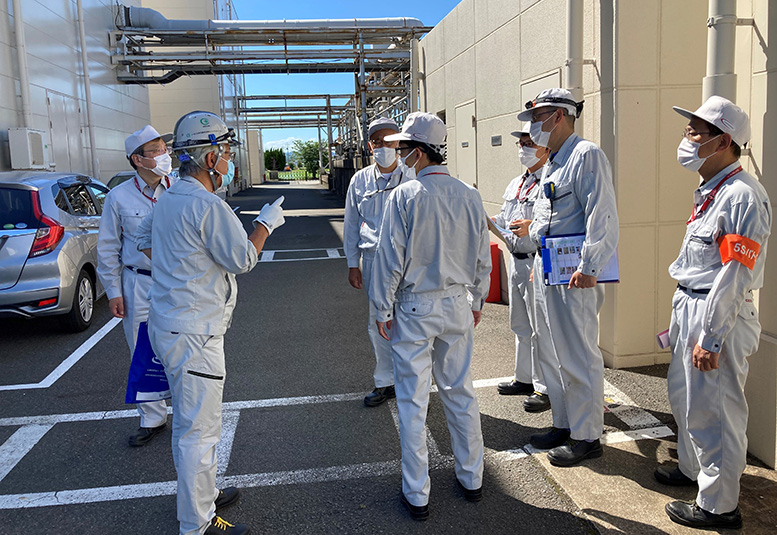
Traffic Safety Initiatives
Regardless of whether vehicles are being operated for business, commuting or private purposes, traffic accidents can have a huge negative impact on family life and disrupt company operations. Therefore, we have set the critical target of zero at-fault traffic accidents for our employees. We send out timely information and conduct training that covers daily safe driving tips based on the traffic safety plan and practices we formulate each year.
Traffic Safety Initiatives
◇ Participation in various events
- The 200-Day Challenge— No Accidents, No Violations
- Smart Commute in Okayama prefecture
- Prefectural traffic safety campaigns, etc.
◇ Working with other organizations
- Training carried out by police officers from local police stations with jurisdiction over our business locations
- Hands-on traffic safety training carried out by local police.
- Traffic safety seminars conducted for new employees by JAF and traffic schools.
◇ Maintaining equipment on company vehicles
- Installation of drive recorders for all company vehicles to prevent harm caused by erratic driving, etc.
- Installation of alcohol breathalyzers in all company vehicles to eradicate drunk driving, and more.
◇ Sending out timely information and promoting awareness activities
- Sending out information and conducting awareness activities by the health and safety committees in each area
- Company-wide rollout and internal notices with bulletins and information on traffic hazard areas, etc.
In fiscal 2023 and beyond, we will continue to create an environment where employees can work safely.
Awards
- Received awards from the police, prefecture and district in fiscal 2017, 2018 and 2020 for traffic safety activities
- Received the Smart Commuting Okayama Grand Prize for the third consecutive year in 2020, received Okayama District Grand Prize in 2021, GOOD ROUTE in 2022 (Video interview about our initiatives published online)