What are aliphatic epoxy resins?
Aliphatic epoxy resins are formed by glycidyl ether (or ester) of aliphatic alcohols or carboxylic acids. There are two types of aliphatic epoxy resins: linear and cyclic. Each possesses characteristics, such as flexibility and weather resistance, derived from its aliphatic origin.
This article explains the properties and uses of aliphatic epoxy resins and compares them with other epoxy resins.
Main characteristics of aliphatic epoxy resins
In addition to the characteristics of epoxy resins, aliphatic epoxy resins also have a variety of other properties depending on the characteristics of the aliphatic group and the number of functional groups.
Listed below are some representative characteristics.
Flexibility and toughness
Aliphatic epoxy resins possess flexibility and toughness. They have flexible chemical bonds compared to aromatic epoxies’ rigid chemical bonds. Curing allows them to act like rubber, even within the cross-linked structure. Therefore, when added to thermosetting resins, they can impart flexibility, creating resilient resins that do not easily break even when bent.
Chemical resistance
Chemical resistance is achieved through the dense structure created by aliphatic epoxy resins. The cross-linked structure formed by the epoxy resin effectively prevents resin deformation caused by chemicals and water, resulting in chemical resistance.
Heat resistant
Aliphatic epoxy resins have excellent heat resistance and high-temperature properties. Especially in the case of aliphatic epoxy resins with multiple functional groups, they form a robust three-dimensional cross-linked structure upon curing, which enhances heat resistance. This makes them suitable for use in high-temperature environments and applications.
Applications of aliphatic epoxy resins
Aliphatic epoxy resins, with their various properties, are primarily used as coatings, adhesives, reactive diluents, and resin stabilizers. Let’s examine each application in more detail.
Coatings
Aliphatic epoxy resins are often used in coatings to protect and preserve buildings, construction materials, and cultural heritage items. In outdoor areas, where exposure to sunlight, rain, and wind is a concern, enhancing coating durability is crucial; thus, aliphatic epoxies are widely utilized. Among the aliphatic epoxy resins, water-soluble epoxy resins, in particular, can be used for floor coatings.
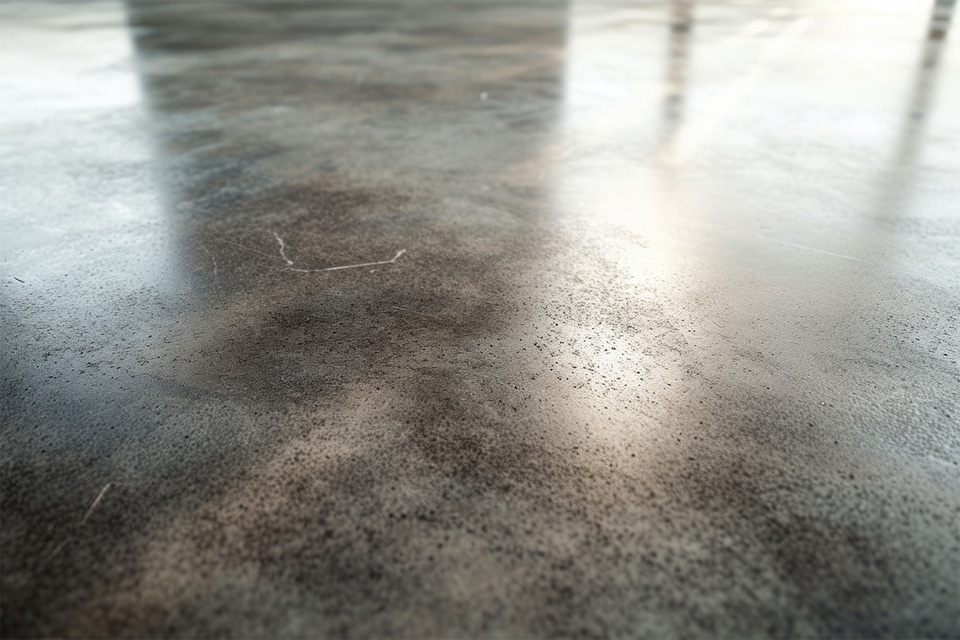
In addition to improving durability, they can reduce VOCs (volatile organic compounds), thus improving indoor environments. As cross-linking agents for floor coatings, they can be considered more environmentally and human-friendly.
Adhesives
Aliphatic epoxy resins are used as adhesives for various materials, including concrete, metal, glass, and wood. They can also be used as adhesives for bonding metals in printed circuit boards. Cross-linking the base resin’s functional groups with aliphatic epoxy resins can reduce adhesive residues on adhered materials.
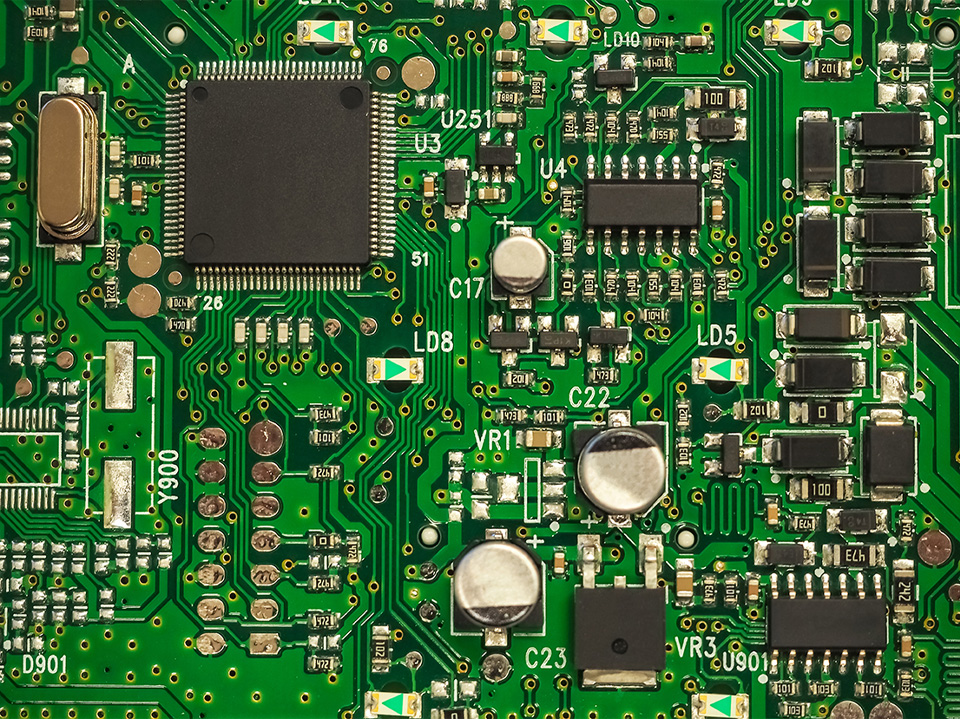
Reactive diluent
Reactive diluents dilute high-viscosity resins, adjusting them to low viscosity to improve workability. Adding them to paints and coatings can help attain the desired viscosity and make time-consuming tasks smoother. Moreover, because the diluents have reactive functional groups, they are incorporated into the curing system without the need to remove solvents during curing.
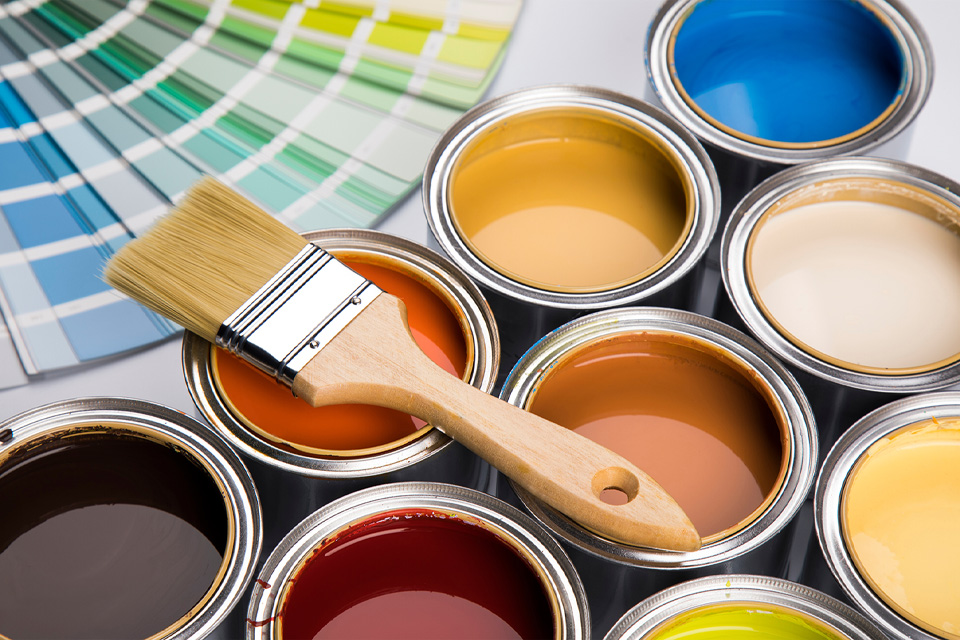
Related article
Resin stabilizer
Resin stabilizers are used to prevent degradation during molding and the usage of resins. Several causes of degradation can be found, including the generation of chlorine and acid corrosion. Resin stabilizers can function as chlorine catchers to prevent the degradation of chlorine-based resins and can also capture hydrochloric acid, protecting against degradation and corrosion caused by acids.
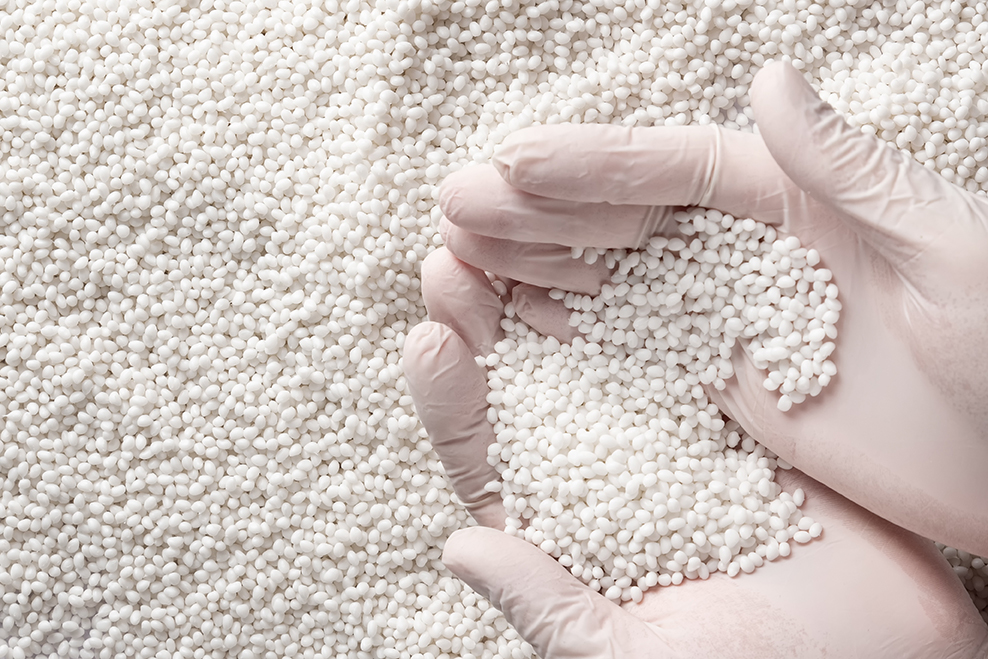
Related article
Comparison with other epoxy resins
Here are some other types of epoxy resins, their characteristics, and their comparison with aliphatic epoxy resins.
Bisphenol-type epoxy resins
Bisphenol A and bisphenol F are common epoxy resins used in various materials.
Overview
This glycidyl ether-type resin can be created by reacting bisphenol A with epichlorohydrin in the presence of a basic catalyst. By changing the ratio of molecular weights during the reaction, different morphologies of epoxy resins can be obtained.
Features
Bisphenol-type epoxy resins share common characteristics with epoxy resins of all types. The basic features include:
- Water resistance
- Corrosion resistance
- Heat resistance
- Chemical resistance
- Moisture resistance
- Weather resistance
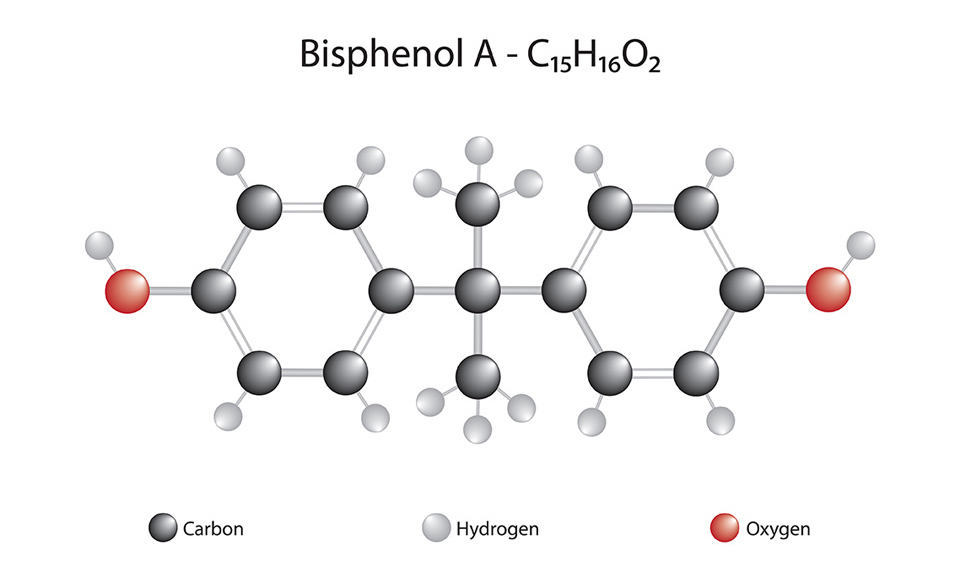
Bisphenol-type epoxy resins are advantageous, as they do not produce by-products during curing, resulting in low-volume shrinkage and high dimensional stability. They also have excellent electrical insulation properties and are stable against acids, alkalis, and salts, providing outstanding chemical resistance.
Novolac-type epoxy resins
Novolac-type epoxy resins have a similar reaction pathway to bisphenol-type epoxy resins, but novolac is used instead of bisphenol.
Overview
These glycidyl ether-type resins are obtained by reacting phenolic novolac with epichlorohydrin. Developed to improve cross-link density, they are also known as cresol novolac-type epoxy resins when phenol is replaced with o-cresol.
Features
Due to the large number of functional groups, novolac-type epoxy resins have a strong cross-linked structure and exhibit excellent heat resistance, chemical resistance, insulation, and hardness. Their structure does not contain VOCs or solvents, which makes them ideal for use as semiconductor encapsulation materials.
Glycidyl amine epoxy resins
These epoxy resins are aminated and glycosylated, including compounds such as tetraglycidyl diaminodiphenylmethane, with four functional groups, and triglycidyl-p-aminophenol, with three functional groups.
Overview
These highly reactive epoxy resins are glycidyl ether compounds obtained by reacting epichlorohydrin with aromatic amines. Their tendency to self-polymerize is a drawback. They can be cured without hardeners or catalysts, leading to a shorter shelf life.
Features
They have low viscosity and relatively low molecular weight at room temperature, and their multifunctionality results in a high glass transition temperature. The C-N bonds in glycidyl amine-type epoxy resins have lower bond energy than C-C or C-O bonds, resulting in a lower thermal decomposition temperature.
Aliphatic epoxy resin, DENACOL
DENACOL is a special epoxy resins developed by Nagase ChemteX using their advanced and unique organic synthesis technology. DENACOL's typical products are aliphatic epoxy resins. It offers a broad lineup ranging from monofunctional to multifunctional aliphatic epoxy resins, allowing selection based on specific properties.
In particular, many water-soluble epoxy resins have been developed. These are VOC-free, making them suitable for fiber and paper manufacturing sites for water-based processing applications. Besides water, they also have high solubility in solvents, allowing them to be used as cross-linking agents in multiple systems.
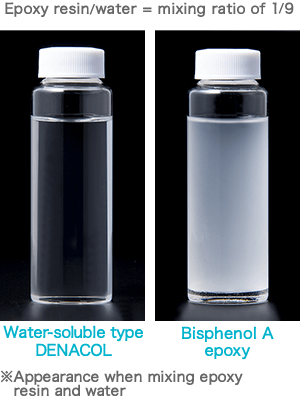
DENACOL is classified into three types based on the number of epoxy groups: mono-functional, di-functional, and multi-functional.
Mono-functional type
Mono-functional types are epoxy resins with a mono-functional structure, such as phenol and 2-ethylhexanol, as the main skeleton. They can be used as adhesive improvers or reactive diluents. The mono-functional types are particularly expected to provide functionalities different from cross-linking reactions.
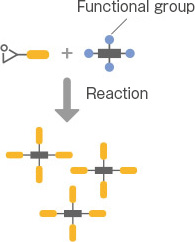
Di-functional type
Di-functional types are epoxy resins with a di-functional structure, such as polyethylene glycol, polypropylene glycol, butanol, and benzene-1,3-diol, as the main skeleton. They can be used as water-soluble resin or electronic material cross-linking agents. Using di-functional types can yield curing agents that reduce brittleness and provide flexibility due to changes in cross-link density.
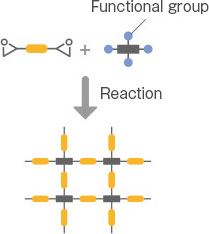
Multi-functional type
Multi-functional types are epoxy resins with multi-functional structures, such as sorbitol and glycerin, as the main skeleton. They can be used as cross-linking agents, viscosity modifiers, or for surface treatment of fibers. The strong, three-dimensional cross-linked structure with the base material and epoxy groups can enhance dimensional stability and heat and chemical resistance.
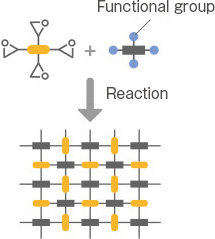