Semiconductor encapsulation material(Liquid Molding Compound)
Our semiconductor encapsulants are used in advanced semiconductor fields, contributing to the acceleration of computational processing, energy efficiency, and miniaturization of various devices, thereby contributing to the realization of a super-smart society.
Flexible supply form
LMC
Liquid Molding Compound
- ・Mass production track record for WLP
- ・Warpage control
- ・High flowability (narrow gap penetration)
- ・Low temp molding (125°C IMC)
a-SMC
advanced-Sheet Molding Compound
- ・Warpage control
- ・High flowability (narrow gap penetration)
- ・Improved MUF performance
- ・Chemical resistance
- ・High toughness
- ・compatible with panel process
General IC
CUF:Capillary Under Fill
- ・High penetration speed even with narrow gaps
- ・No flow marks after curing
- ・High heat resistance
- ・High moisture resistance
- ・High moisture reflow resistance
- ・High purity
- ・Low alpha ray
Changing needs for encapsulating materials
Supporting highly integrated packaging roadmap
We provide optimal encapsulation solutions for the most advanced semiconductor packaging technologies.
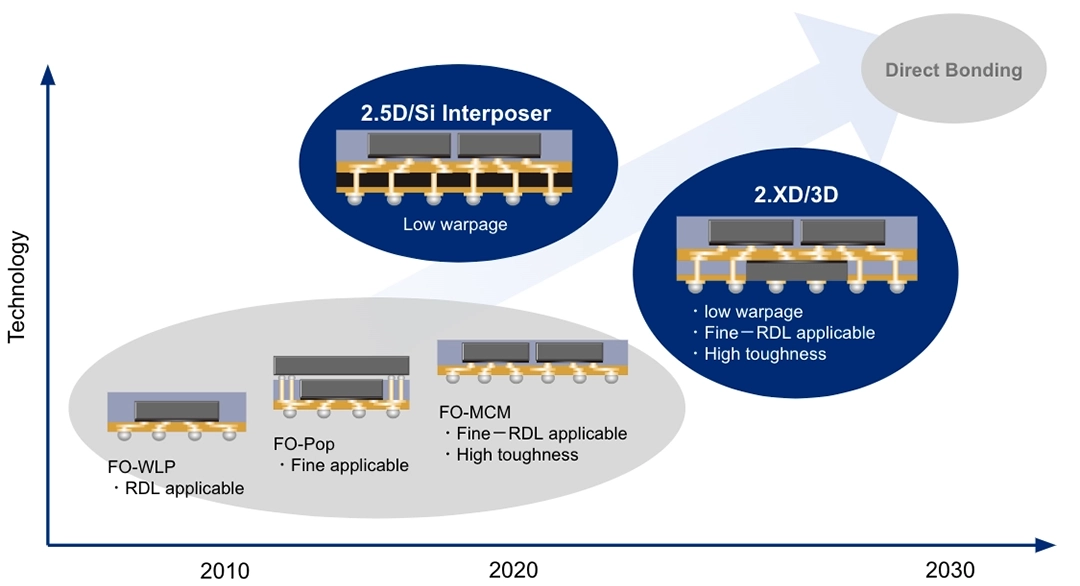
Innovation in encapsulation materials
Solving various issues in plastic packaging with material technology
As semiconductor devices become more and more complex, packaging challenges vary from customer to customer. We will address a wide range of challenges based on the epoxy resin modification technologies we have developed over the years.
Increased complexity of
semiconductor package structures
Functions required for
semiconductor encapsulants
semiconductor package structures
semiconductor encapsulants
Warpage control
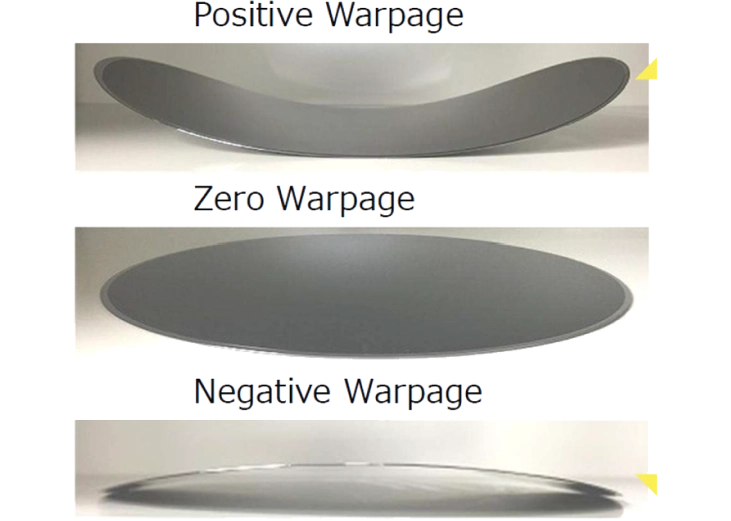
Filling performance
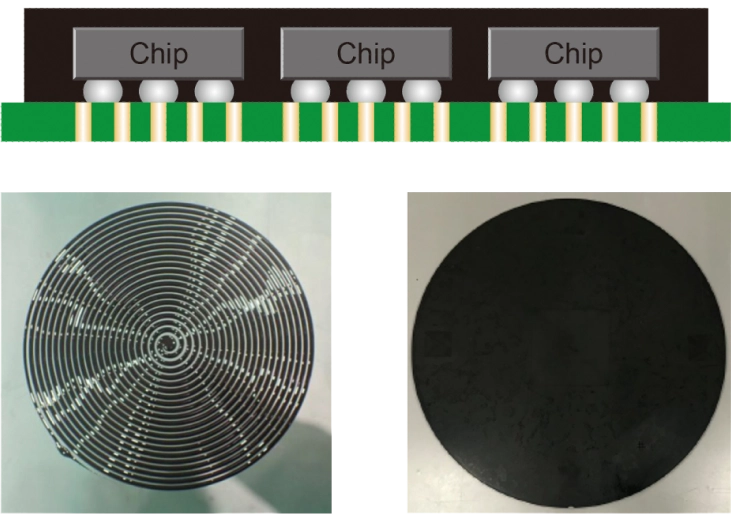
Reliability
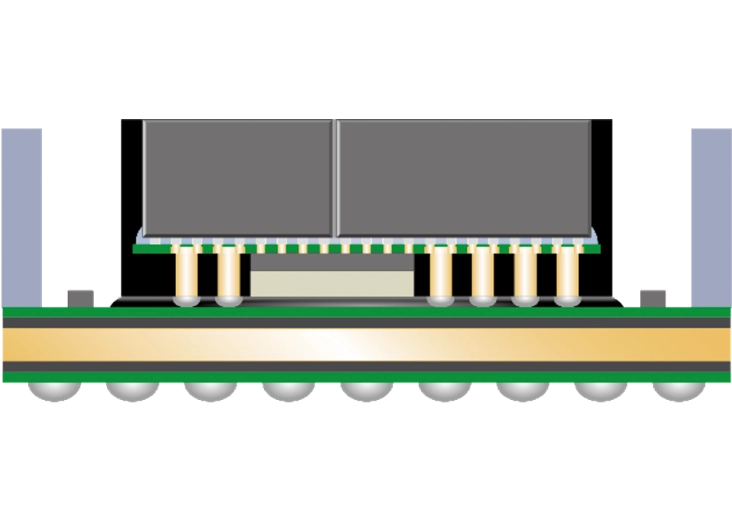
Typical Processes
1. Dispensing and application
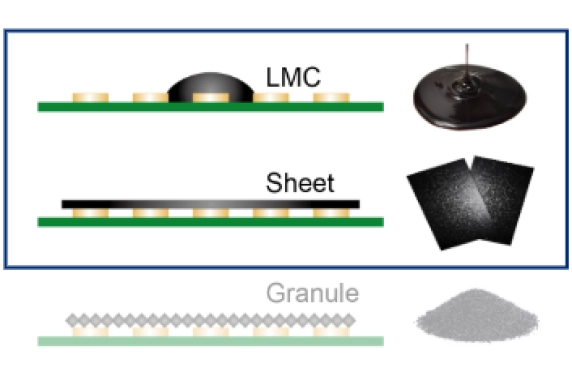
2. Setting
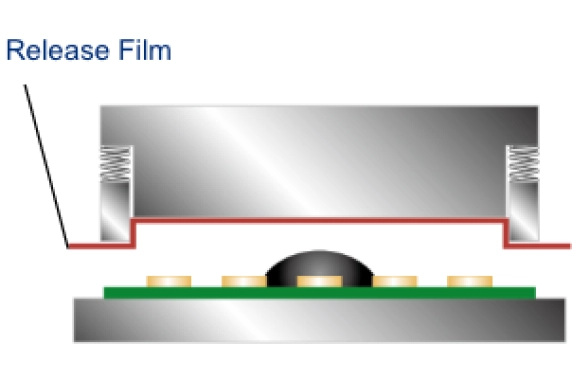
3. Suction and decompression
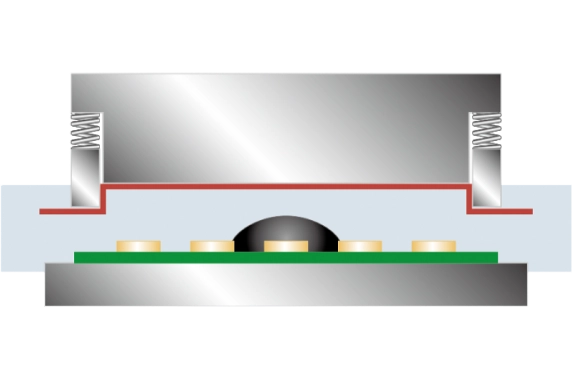
4. Increasing pressure
4MPa / 125℃ / 10min
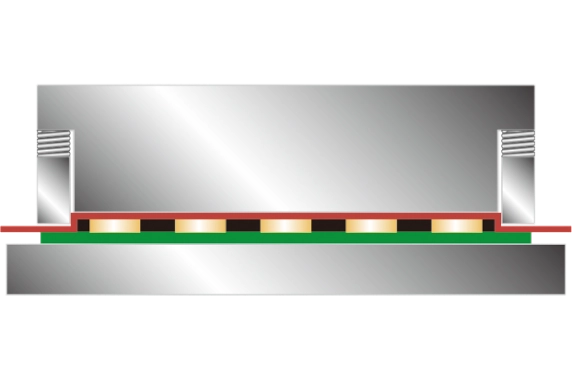
5. Demolding
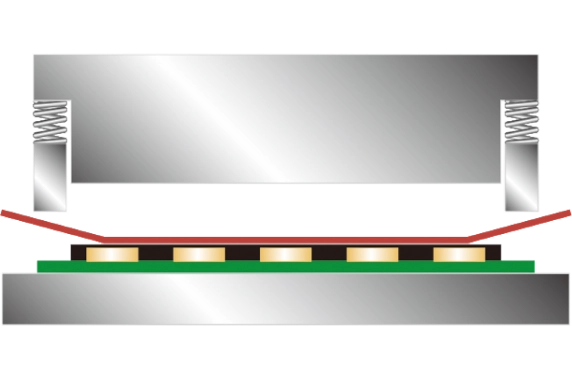
6. Curing
150℃ / 60min
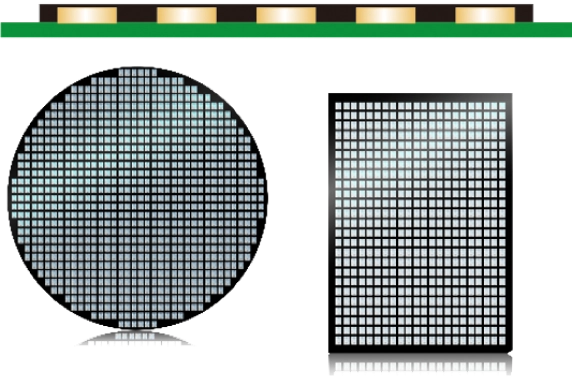
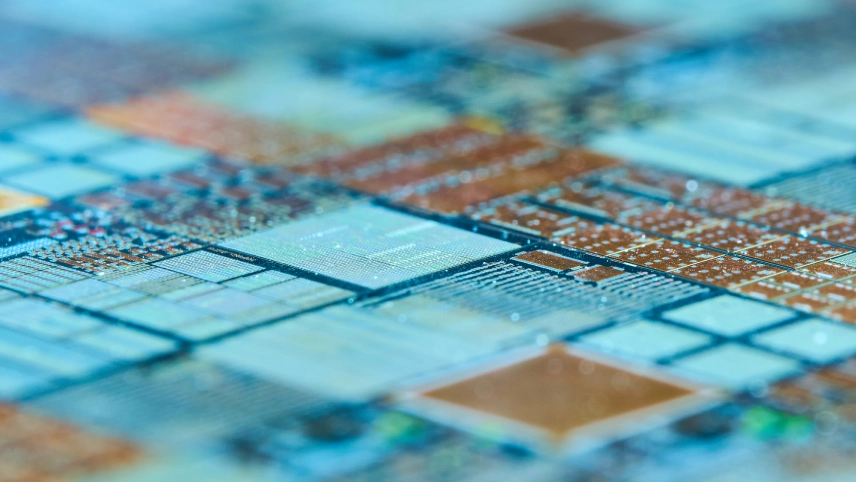