Characteristics of silicone rubber (elongation, strength, shock absorption) and comparison with other materials
Characteristics of silicone rubber
Silicone rubber is a synthetic rubber having stable elasticity and weather resistance in a wide temperature range. It has relatively high elongation performance and is widely used as a shock absorber and sealing material, but its tensile strength may be slightly lower than that of other rubbers. In addition, due to the slightly sticky surface, friction tends to occur easily in a dry state. Because it is resistant to temperature changes and retains the flexibility even under high temperatures, it is used in a wide range of purposes from the medical and food fields to automotive parts and electronic equipment. It also has excellent weather resistance and electrical insulation properties, and the moderate surface friction prevents slippage. However, when requiring sliding, it is necessary to have a special surface treatment and material selection. At the same time, the sealing surface has a feature of sufficient airtightness, so it is expected to be used in a variety of fields.
*Please note that the values presented in this ranking are general guidelines only. Actual values may vary significantly depending on the manufacturer, specific grade, and formulation.
Comparison of silicone rubber and other materials ① Elongation rate
Silicone rubber has a relatively broad elongation property range of 200-800%, however, compared to mechanically tough rubbers such as urethane, it may be less strong at the same elongation.
Although it is not far different from EPDM and NBR, silicone rubber has the advantage of being less temperature-dependent so that it is easier to maintain elongation at extreme low and high temperatures.
Although it is not far different from EPDM and NBR, silicone rubber has the advantage of being less temperature-dependent so that it is easier to maintain elongation at extreme low and high temperatures.
Rubber-Like Resin has an extremely wide elongation range of 300-1,000% and it will be a strong choice when large deformation is required.
Silicone rubber (200-800%) and EPDM (200-600%) also have high elongation. Especially silicone rubber is particularly superior in that its elongation rate does not change much with temperature change.
Elongation range of NBR is 200 to 500% and that of urethane rubber is 200 to 600%, both are in the standard range, but urethane rubber is characterized by properties of both high elongation and strength.
Elongation rage of fluoro rubber is 150-300%, which is slightly lower, but it is chosen for purposes that require high heat resistance and chemical resistance.
Silicone rubber (200-800%) and EPDM (200-600%) also have high elongation. Especially silicone rubber is particularly superior in that its elongation rate does not change much with temperature change.
Elongation range of NBR is 200 to 500% and that of urethane rubber is 200 to 600%, both are in the standard range, but urethane rubber is characterized by properties of both high elongation and strength.
Elongation rage of fluoro rubber is 150-300%, which is slightly lower, but it is chosen for purposes that require high heat resistance and chemical resistance.
Comparison of silicone rubber and other materials ② Tensile strength
Silicon rubber is in the medium or slightly lower strength range. Urethane rubber has extremely high strength, and NBR and fluoro rubber also often show higher strength values than silicone rubber. In addition, silicone rubber is often chosen for the overall balance of heat resistance, weather resistance and electrical properties. In many cases, when looking at pure mechanical strength, other rubbers are more superior.
Urethane rubber (20-50 MPa) has a significantly high tensile strength and it is suitable for areas with heavy mechanical loads.
NBR (10 to 20 MPa), EPDM (7 to 21 MPa) and fluoro rubber (10 to 20 MPa) have moderate tensile strength and also have general-purpose strength and respective resistance.
The tensile strength of silicone rubber (5-10 MPa, up to 15 MPa as highest) tends to be slightly inferior in terms of pure strength. However, other properties of silicone rubber, such as heat resistance and electrical insulation performance, are often recognized.
The tensile strength of RLR (6 to 30 MPa) has a wide range and may improve to a level similar to urethane rubber in high-strength products of rubberlike resins.
NBR (10 to 20 MPa), EPDM (7 to 21 MPa) and fluoro rubber (10 to 20 MPa) have moderate tensile strength and also have general-purpose strength and respective resistance.
The tensile strength of silicone rubber (5-10 MPa, up to 15 MPa as highest) tends to be slightly inferior in terms of pure strength. However, other properties of silicone rubber, such as heat resistance and electrical insulation performance, are often recognized.
The tensile strength of RLR (6 to 30 MPa) has a wide range and may improve to a level similar to urethane rubber in high-strength products of rubberlike resins.
Comparison of silicone rubber and other materials ③ Shock absorption
The surface of silicone rubber has a unique sticky feel and often feels even stickier on the contact surface with the other material. If fluidity and sliding are more important, NBR, urethane rubber or coated rubber would be better to be chosen. On the other hand, silicone rubber may be better choice when you want to use it as a non-slippery material.
Comparison by loss factor (tanδ)
The loss factor of rubberlike resin (0.9) is an extremely high value, and it has very high vibration and shock damping capabilities.Silicone rubber (0.2 to 0.4) and urethane rubber (0.2 to 0.5) have moderate loss factors and have both standard vibration damping and elasticity.
NBR, EPDM and fluoro rubber have loss factors of 0.1 to 0.3 and tend to have relatively low energy loss and have resistance to dynamic loads such as continuous deformation.
Comparison by resilience modulus
Urethane rubber (50-80%) has a very high resilience modulus and is heavily used in fields requiring high bounce and dynamic performance.Silicone rubber (30-50%) has the advantage that its resilience modulus is easy to maintain stable elasticity in a wide temperature range.
The resilience modulus of NBR and EPDM ranges from 30 to 70% depending on the purpose and compound. They have well-balanced elasticity.
Fluoro rubber (20-50%) has a medium resilience modulus, but the strength of this material is environmental resistance, which maintains elasticity even under severe environmental conditions.
RLR (4.5%) has significantly lower resilience, but may be suitable for vibration insulators and shock absorber materials because it absorbs shock but does not rebound easily.
【Summary】Comparison of silicone rubber and other materials
Comparing these six materials, first of all, in terms of elongation (elongation at break) and tensile strength, urethane rubber stands out for the high mechanical strength (20 to 50 MPa). On the other hand, rubberlike resin has a wide range of elongation (6 to 30 MPa) and a large elongation (300 to 1,000%), which means that it may be as strong as urethane depending on the application.
Silicone rubber has a wide elongation range of 200 to 800% and it is highly responsive to temperature changes, however, its tensile strength is only 5 to 10 MPa (about 15 MPa even for high-strength grades), which is often lower than nitrile rubber, EPDM and fluoro rubber (all about 10 to 20 MPa). In terms of coefficient of friction, while silicone rubber has a slightly higher coefficient of friction of 0.5 to 1.0, NBR, EPDM and urethane rubbers all have standard sliding properties of around 0.3 to 0.7, and fluoro rubber can make even lower friction by coating or compounding.
In terms of loss factor (tanδ) and resilience modulus, Rubber-Like Resin has an extremely high loss factor of 0.9, which provides excellent vibration absorption and shock mitigation properties in combination with an extremely low resilience modulus of 4.5%. On the other hand, silicone rubber has a tan δ of 0.2-0.4 and a repulsive modulus of 30-50%. Therefore, it has both good elasticity and damping performance. Nitrile rubber and EPDM have a similar balance to silicone rubber. Urethane rubber has a slightly higher tan δ of 0.2 to 0.5 and a very high resilience of 50 to 80%. It is suitable for applications requiring mechanical strength and for parts subjected to repeated impacts. Fluororubber has moderate elongation and elasticity, but it is highly valued for the ability to resist high-temperature environments and strong chemicals, and is selected when reliability under severe conditions is important. In general, it is important to select the optimal material by combining the characteristics of each material based on the performance required, such as heat resistance, electrical insulation, mechanical strength, and shock absorption.
Silicone rubber has a wide elongation range of 200 to 800% and it is highly responsive to temperature changes, however, its tensile strength is only 5 to 10 MPa (about 15 MPa even for high-strength grades), which is often lower than nitrile rubber, EPDM and fluoro rubber (all about 10 to 20 MPa). In terms of coefficient of friction, while silicone rubber has a slightly higher coefficient of friction of 0.5 to 1.0, NBR, EPDM and urethane rubbers all have standard sliding properties of around 0.3 to 0.7, and fluoro rubber can make even lower friction by coating or compounding.
In terms of loss factor (tanδ) and resilience modulus, Rubber-Like Resin has an extremely high loss factor of 0.9, which provides excellent vibration absorption and shock mitigation properties in combination with an extremely low resilience modulus of 4.5%. On the other hand, silicone rubber has a tan δ of 0.2-0.4 and a repulsive modulus of 30-50%. Therefore, it has both good elasticity and damping performance. Nitrile rubber and EPDM have a similar balance to silicone rubber. Urethane rubber has a slightly higher tan δ of 0.2 to 0.5 and a very high resilience of 50 to 80%. It is suitable for applications requiring mechanical strength and for parts subjected to repeated impacts. Fluororubber has moderate elongation and elasticity, but it is highly valued for the ability to resist high-temperature environments and strong chemicals, and is selected when reliability under severe conditions is important. In general, it is important to select the optimal material by combining the characteristics of each material based on the performance required, such as heat resistance, electrical insulation, mechanical strength, and shock absorption.
RLR (Rubber-Like Resin): A Revolutionary Material Combining High Tensile Strength and Elongation
Traditional resin materials have struggled to balance flexibility and durability. To overcome this challenge, we've developed Rubber-Like Resin (RLR), which combines rubber-like flexibility with exceptional durability.
This innovative material features superior elasticity and scratch resistance, while also providing excellent vibration absorption and chemical resistance. Since it cures at room temperature, no heating furnace is required—contributing to energy efficiency. RLR can be utilized across diverse applications, from electronic component coatings to construction materials and automotive parts.
This innovative material features superior elasticity and scratch resistance, while also providing excellent vibration absorption and chemical resistance. Since it cures at room temperature, no heating furnace is required—contributing to energy efficiency. RLR can be utilized across diverse applications, from electronic component coatings to construction materials and automotive parts.
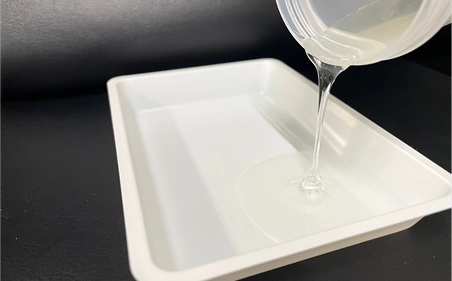
Key Advantages of Rubber-Like Resin Compared to Urethane Materials
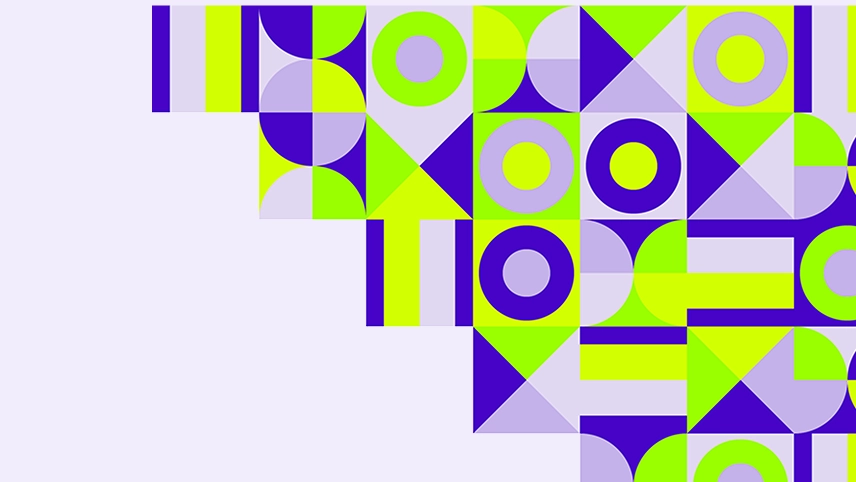