Study on Drying Rate During Curing and Glass Transition Temperature of Cured Epoxy Resins Using DENACOL EX-614B and GREEN DENACOL GEX-614B
In this experiment, a comparative evaluation of the drying speed and Glass Transition Temperature (Tg) was conducted for two cases: drying a typical bisphenol A-type epoxy resin with amine, and drying the same bisphenol A-type epoxy resin with the addition of DENACOL EX-614B (a sorbitol-based epoxy) and GREEN DENACOL GEX-614B (also a sorbitol-based epoxy, derived from plant-based materials).
Comparative Evaluation of Drying Speed
A comparative evaluation was conducted to examine how the presence or absence of DENACOL and GREEN DENACOL affects the drying speed.
Mixing ratios were set as follows.
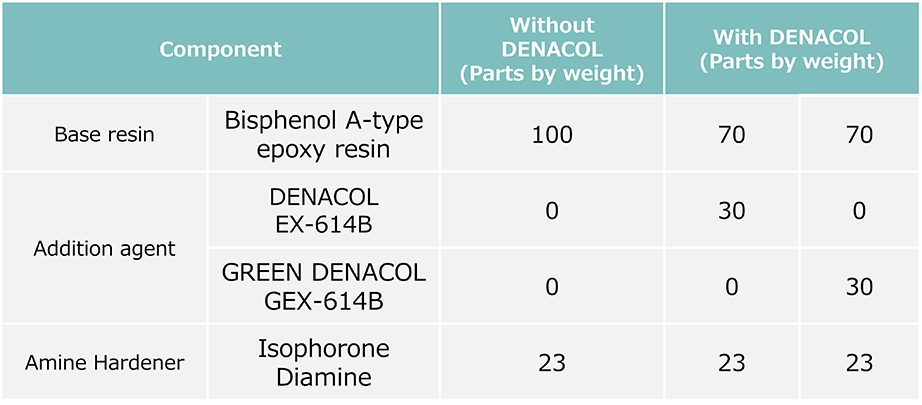
【Result】
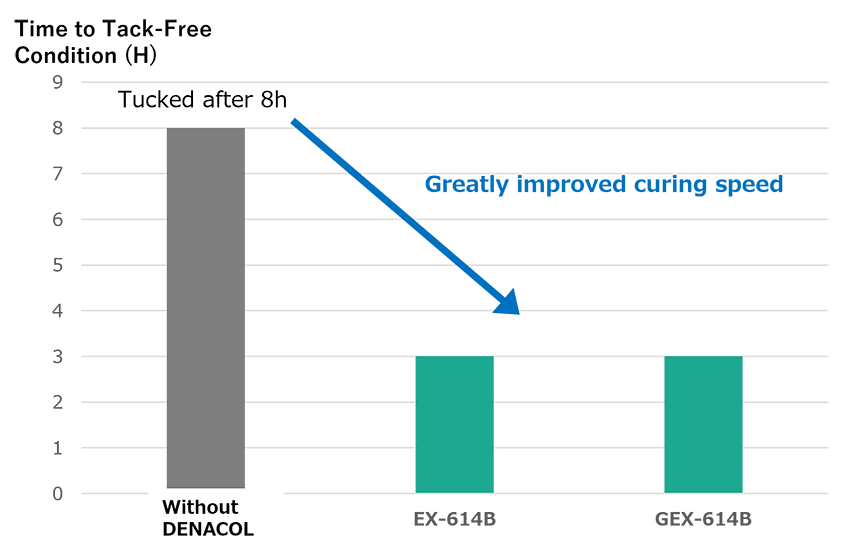
- Evaluation Composition :
- Epoxy Resin, Amine Hardener (Isophorone Diamine), Methyl Ethyl Ketone
- Drying Conditions :
- Room Temperature (20℃ to 25℃)
- Evaluation Method :
- Coated onto a glass substrate and measured the time until the surface tackiness disappeared
Figure 1. shows the measurement results of the drying time during drying at room temperature after application to a glass substrate. When only a typical bisphenol A-type epoxy resin was used, the coating surface remained tacky even after 8 hours, indicating insufficient drying.
In contrast, when an epoxy resin consisting of a 7:3 mixture of bisphenol A-type epoxy resin and DENACOL EX-614B or GREEN DENACOL GEX-614B was used, the coating surface became tack-free within approximately 3 hours after application, demonstrating sufficient drying progress.
This improvement in drying speed is attributed to the multifunctional structure of EX-614B and GEX-614B, which possess multiple epoxy groups in their molecular. Furthermore, it was confirmed that GEX-614B, a highly bio-based epoxy compound derived from plant-based materials, exhibits performance comparable to that of EX-614B.
Comparison of the Glass Transition Temperature(Tg)
Next, a comparative evaluation was conducted to examine how the presence or absence of DENACOL and GREEN DENACOL affects Tg.
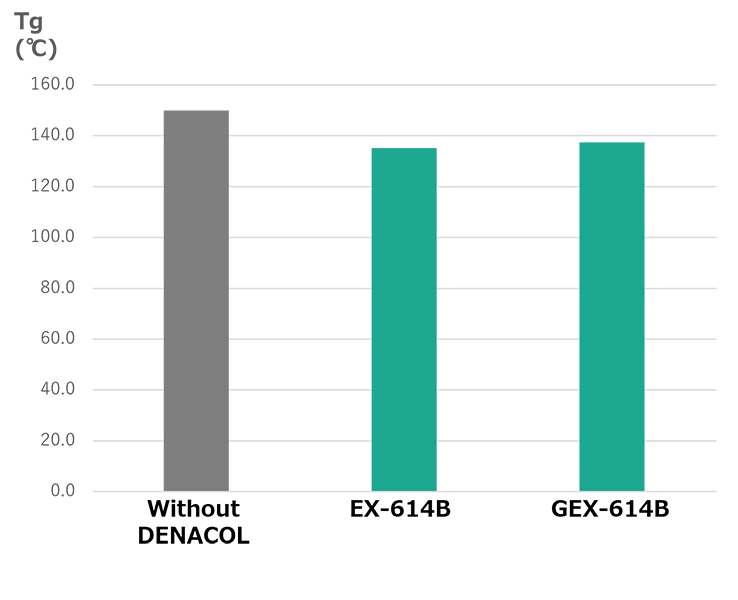
- Evaluation Composition :
- Epoxy Resin, Amine Hardener (Isophorone Diamine), Methyl Ethyl Ketone
- Drying Conditions :
- 80°C for 4 hours → 150°C for 1 hour
- Evaluation Method :
- Coated onto an aluminum plate, and Tg of the coating film was measured.
Figure 2. shows the results of measuring Tg under the curing conditions specified in Table 1. after sufficient thermal curing. When using bisphenol A-type epoxy resin, Tg was approximately 150°C. In contrast, when an epoxy resin composed of a 7:3 mixture of bisphenol A-type epoxy resin and DENACOL EX-614B or GREEN DENACOL GEX-614B was used, Tg decreased by approximately 15°C.
This decrease in Tg can be attributed to the flexible aliphatic backbone of DENACOL EX-614B and GREEN DENACOL GEX-614B, compared to the rigid aromatic structure of bisphenol A-type epoxy resin.
These findings suggest that using DENACOL or GREEN DENACOL can shorten drying times and enable drying at lower temperatures, offering advantages such as improved production efficiency and reduced energy consumption. However, Tg is lower compared to formulations with aromatic epoxies, making it necessary to optimize the formulation to meet the desired Tg requirements.