プラスチック情報館
3Dプリンタの普及がモノづくり改革を加速する
3Dプリンタとは
近年、3D(3次元)プリンタは、モノづくりを変革する画期的なツールとして注目を集め、製造現場を中心にさまざまな分野で普及しつつあります。
3Dプリンタとは、3DのCADデータをもとに立体の造形物を製作する出力装置です。2次元のプリンタ(印刷機)と使 い方が似ていて、そのわかりやすさから「3Dプリンタ」という呼称が定着していますが、製造現場で使われる場合は、付加製造(Additive Manufacturing)技術と言われています。つまり、今後のモノづくりのキーテクノロジーであることを意味しています。
3Dプリンタの歴史
意外に知られていない事実ですが、3Dプリンタを最初に考案したのは日本人でした。1980年、当時、名古屋市工業研究所に勤務する小玉秀男氏が光造形法を考案し、「立体図形作成装置」として特許を出願。しかし、これに興味を示す企業は現れず、出願審査請求が行われず失効してしまったとのことです。
この光造形法が失効した1987年、米国の3Dシステムズ社が世界初の3Dプリンタを開発。「SLA 1」として商品化されました。その3年後の1990年には、材料にプラスチックを使い、現在の3Dプリンタの主流の一翼を担う材料押出方式(熱溶解積層法:FDM)による最初の3Dプリンタが米国・ストラタシス社から発売。しかし、当時の3Dプリンタは非常に高価(数百万円レベル)であったため、ユーザーもごく一部に限られていました。
そして、2009年の基本特許の保護期間の終了に伴い、それ以降は3Dプリンタの低価格化が進み、パーソナルユースの3Dプリンタの発売も相次ぎました。
3Dプリンタの爆発的な普及の契機となったのは、2013年に米国の技術情報誌「Wired」の元編集長・クリス・アンダーソン氏の著書「MAKERS―21世紀の産業革命が始まる」の出版でした。ベストセラーとなった同著では、3Dプリンタの普及が従来の製造業のパラダイムシフトを加速すると記されていたことから3Dプリンタ人気が急騰。以来、パーソナルユース向けのローエンド機から、本格的な製造に対応したハイエンド機まで、さまざまな価格帯の3Dプリンタが発売され、現在に至っています。
3Dプリンタの種類
米国の工業規格の認証機関・ASTMインターナショナルが設定した「ASTM規格」では、プリンタを付加製造 (Additive Manufacturing)と呼称し、以下の7つの方式を規定しています。
3Dプリンタ(付加製造:(Additive Manufacturin)の7つの方式(ASTMによる分類)
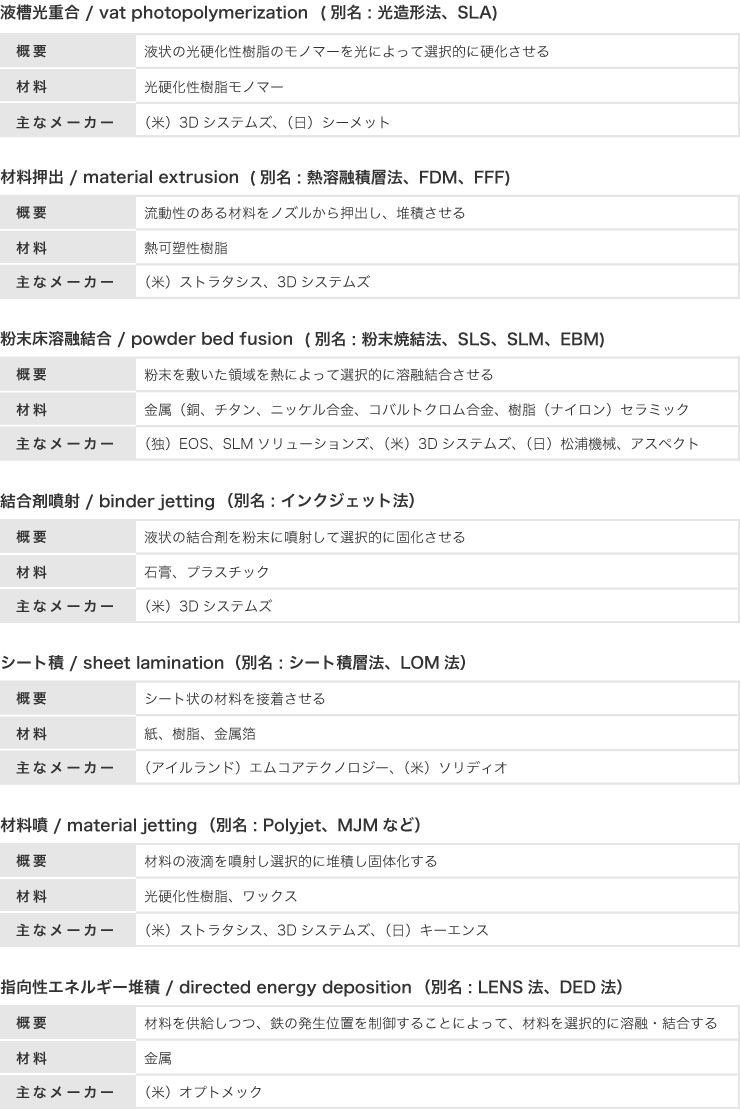
この7つの方式の内、現在、材料押出方式(熱溶解積層法)と、材料噴射方式が製造現場で最も普及しているタイプであり、双方とも主材料にプラスチック(材料押出:熱可塑性樹脂/材料噴射:光硬化性樹脂)が使われています。
3Dプリンタの活用法
多品種少量生産に最適な3Dプリンタは、製品開発・製造現場を中心に、さまざまなシーンで活躍しています。
モックアップ
製品企画の段階でモックアップ(立体模型)を製作できれば、製品の完成イメージを共有が可能。特にプレゼンテーションなどで訴求力を高めます。
試作(プロトタイプ)
製品の開発・設計段階で、製品や部品の評価に使われる試作品製作に用いれば、繰り返しの試作にも容易に対応し、評価の効率化、低コスト化にも貢献します。
型
耐熱性の高い樹脂(エンプラ、スーパーエンプラ)を材料に使えば、成形品に用いられる型の製作も可能です。
治具
治具とは製造ラインや個人向けにカスタマイズされたオリジナルの工具です。3Dプリンタでは、複雑な形状や設計変更にも短時間で自在に対応し、製造現場での作業の効率化にも貢献します。
建築模型
建物の構造や外観を忠実に再現したミニチュアモデルを作成し、工法の評価・検討や施工主へのプレゼンテーションにも役立ちます。
マスカスタマイゼーション
義歯、補聴器などの医療用機器に代表されるカスタマイズ製品の低コストでの一品製作などに最適です。
3Dプリンタの導入メリット
多品種少量生産に最適な3Dプリンタは、製品開発・製造現場を中心に、さまざまなシーンで活躍しています。
開発期間を大幅に短縮
従来、外注に依存していた部品や製品の試作品の製作に3Dプリンタを活用すれば、設計変更にも自在に対応できるば かりではなく、試作品の製作期間の大幅な短縮化も可能。また、製造段階では一部の型製作にも対応し、製品企画・開発から量産化までの期間の短縮化に貢献します。
コスト削減
これまで多くのコストが発生していた部品設計や型設計段階から試作品段階での仕様変更、作り直しにも容易に対応するため、設計・製造に要するコスト全体を削減します。
多品種少量生産に最適
比較的需要は少ないながらも重要なリペア用部品やカスタム品など少量生産に最適です。大量生産品とのトータルコストの比較は、品種にもよりますが、概ね1,000個レベルのロッドが損益分岐点とされています。
生産の多様化に対応
3Dプリンタは設置した場所が即生産場所となるというのも大きな特長です。例えば、店舗やリペアセンターなど顧客接点に3Dプリンタを設置し、遠隔地の設計部署から3DCADデータを送れば、その場での出力(生産)が可能となり、在庫ストックや輸送費も不要となります。まさにIoT時代にふさわしいフレキシブルな生産システムを構築します。
導入事例
カメラメーカー・A社の事例
3Dプリンタによるサービスパーツ供給を実現し、コストと納期を削減。
【導入の背景】
A社が過去に発売したデジタルカメラの人気シリーズは、すでに製造・販売を終了。また、サービスパーツの保管期間も終了し、金型も破棄していました。しかし、その後もユーザーからのパーツのオーダーが相次ぎ、対応に苦慮していました。
【対応】
パーツのニーズはあるものの大量に生産する物でもなく、金型を新規に起こすような多額投資は避けたいと考えたA社は、パーツを3Dプリンタで製作する方法を検討。試行錯誤した結果、従来の金型部品と同等の品質でのパーツ供給を実現しました。
【導入後】
多くのユーザーからのニーズに対応することができました。1,000個以内の生産であれば、金型を更新するよりも3Dプリンタの方が製造コストを削減できることを確認。当然、金型の維持・管理コストも不要です。
また、将来的に3Dプリンタを販売店やサービスセンターなどに設置すれば、輸送コストの削減や迅速なパーツ供給によるユーザーサービスの向上にも期待されています。
ケーブルメーカー・B社の事例
3Dプリンタで試作品用樹脂型を造形し、量産用金型製作前の評価に適応。
【導入の背景】
ケーブル端子部分の設計・評価段階では、まずは金型の設計・製作(外注)を経て、完成した試作品を評価し、量産用の金型を仕上げていくプロセスでした。しかし、試作品用・量産用金型の製作には、それぞれ約1ヶ月程度の期間を要し、評価結果によっては金型の再修正のケースも多く、効率化のボトルネックとなっていました。
【対応】
そこでB社では、試作品用金型に代わる樹脂型を3Dプリンタで製作する方法を模索。さまざまな試作品用樹脂型を試作し、ケーブル端末試作品の評価に適応しました。
【導入後】
3Dプリンタによる試作品用樹脂型製作により、約1ヶ月の金型製作期間を大幅に短縮。同時に、試作品評価段階での樹脂型の改良を何度も繰り返すことが可能となったため、量産用金型の品質も向上。結果的に量産用金型の再修正もほとんどなくなり、設計から量産化までの期間を1ヶ月以上短縮し、試作・評価のコスト削減も達成しました。